Webinars

Webinar: Product Strong, High-Performance Parts with SLS 3D Printers
In this exclusive webinar with the Shop3D team, we’ll examine SLS 3D printing, its use cases, and 3D printers and accessories such as Formlabs Fuse 1, Fuse Sift, and Fuse Blast for SLS 3D Printing and post-processing.

Webinar: Start to Finish - Shop3D's Expert Guide to Filament Selection
As a premier 3D printing retailer in Canada for almost 10 years and 3D printing enthusiasts for longer, the Shop3D team has ample experience choosing filaments and knowing which ones work best for specific projects and 3D printers.
That’s why we’re excited to host this webinar, detailing our guide to filament selection. In this webinar, we’ll cover:
- Our favorite filaments and why we love them;
- Overview of various types of filaments;
- Guide to choosing the right filaments
- Best practices for utilizing filaments

Webinar: Simplifying 3D Printing Quoting and Management with AutoQuote3D
AutoQuote3D simplifies and streamlines the time-consuming process of managing 3D printing orders. It is an instant quoting tool that handles all the work, making it easy for customers to instantly know what a print order will cost, while businesses can focus on delivering.
In this webinar, we’ll cover:
- An overview of the AutoQuote3D platform;
- Live demonstration by our team;
- Guest presentation by Felix Izraitel, founder of AutoQuote3D;
- Pricing tiers;
- Answers to commonly asked questions
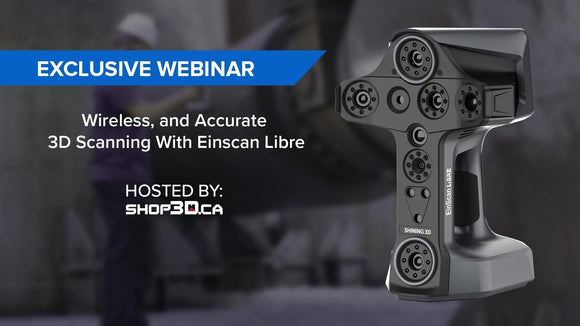
Webinar: Wireless and Accurate 3D Scanning with the Einscan Libre
As far as professional 3D Scanners go, the Einscan Libre is a performance beast. This latest 3D scanning tech combines fully wireless 3D scanning with an all-in-one scanning experience: the ability to complete everything from scan to mesh on the device—no markers necessary. It features one-of-a-kind texture alignment support through its Laser HD mode, and promotes high-level accuracy through its high-performance NVIDIA processor and generous storage.
Join our team for this month’s episode of our exclusive webinar, where we’ll explore the technology behind the Einscan Libre and its limitless capabilities in 3D scanning.
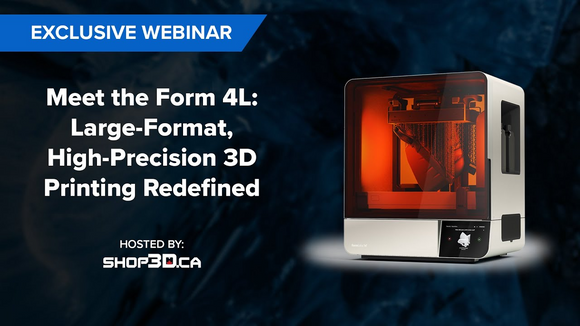
Webinar: Meet the Formlabs Form 4L, Large-Format and High-Precision 3D Printing Redefined
Want to know more and see the Form 4L in action? Then join Chris Lee, Senior Sales Engineer at Formlabs and our team for this exclusive webinar where we explore the capabilities of the Form 4L and how to utilize it to scale production.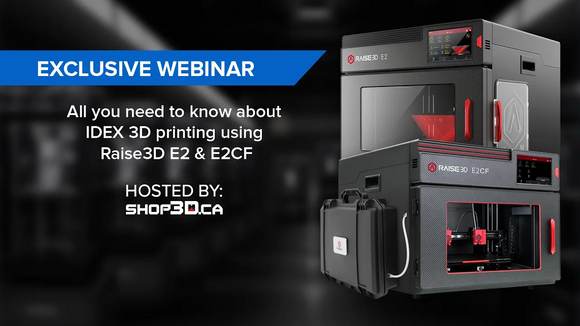
Webinar : All You Need to Know about IDEX Printing Using Raise3D E2 & E2CF
In this edition of our monthly webinar series is dedicated to the IDEX technology and what the different modes mean for professional 3D printing, using the Raise3D E2 and E2CF.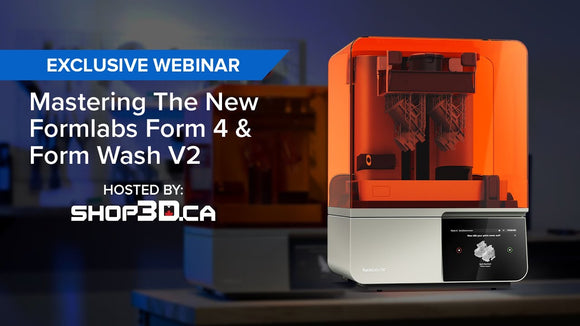
Webinar: Mastering The New Formlabs Form 4 And Form Wash V2
Learn all about this game-changing SLA 3D printer, it's blazing-fast speed, tight tolerance, and accurate printing capabilities. Explore the new and improved Form Wash V2, it’s automated cleaning system and what makes it an essential part of the Form 4 ecosystem.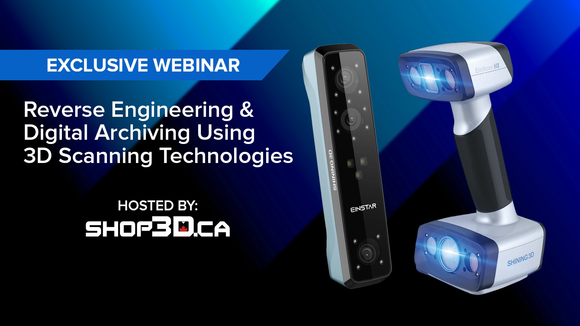
Webinar: Reverse Engineering and Digital Archiving using 3D Scanning Technologies
In this webinar, we'll explore reverse engineering and digital archiving using 3D Scanning technologies. See live demos of Shining 3D's Einstar and Einscan HX, and watch our team discuss their technical capabilities and accuracy levels, 3D Scanning tips, and use case applications. Save your spot now.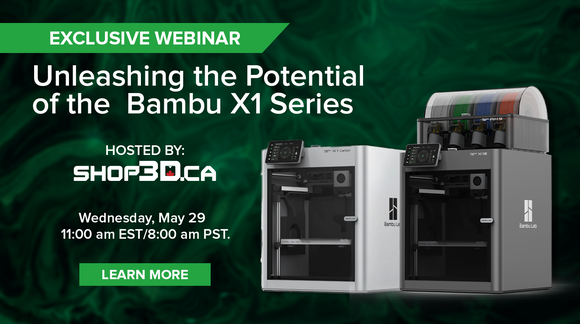
Exclusive Webinar: Unleashing the Potential of the Bambu X1 Series
Get ready to revolutionize your 3D printing experience with the Bambu Lab X1 series in our exclusive webinar. Learn all about the game-changing Automatic Material Systems (AMS) technology and AI failure detection, and explore the key differences between the X1E and X1C.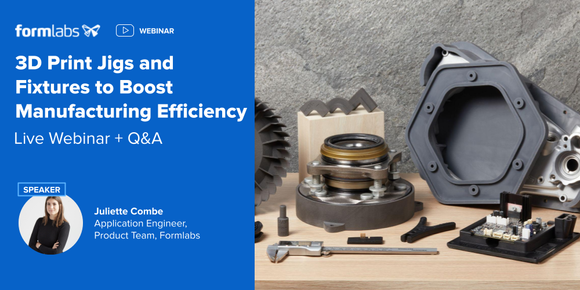
3D Print Jigs and Fixtures to Book Manufacturing Efficiency
Jigs, fixtures, and other manufacturing aids are used by businesses internally to make manufacturing and assembly processes simpler and more reliable, reducing cycle times and improving worker safety. They are vital tools to streamline production workflows and address common problems that arise on the factory floor. With new advances in additive manufacturing technologies and materials you can now replace the standard expensive machined metal jigs and fixtures with lightweight, ergonomic, and part-specific 3D printed tools, with a wide range of materials to enable functional applications. In-house 3D printing enables you to build manufacturing aids rapidly and at a low cost to improve the speed, quality, and efficiency of production. It increases design freedom to build complex, custom tools and encourages continuous improvement. With 3D printed replacement parts, you can grow operational agility, solve day-to-day production issues and reduce machine downtime. Watch this webinar to learn how to quickly 3D print strong, long-lasting tools with SLA and SLS 3D printers that are ready to undergo the rigor of the factory floor, from machining to assembly and inspection. A Formlabs application engineer will guide you through the workflow, share recommendations and delve into real-life examples from innovative companies.
You'll learn:
- How 3D printed jigs and fixtures reduces production costs
- How to design, 3D print, and post-process jigs, fixtures, and replacement parts
- Real-life case studies at every stage of production:
- Fabrication and machining workholding
- Assembly fixtures
- Finishing devices
- Inspections tools
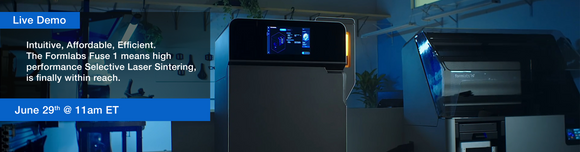