The New Ultimaker S Series Lineup Compared
September 24, 2019
Ultimaker S3: The Ultimate Overview
Akin to the wildly successful launch of the Studio line of Ultimaker printers, the S3 is the little brother to the excellent large-format Ultimaker S5 3D printer. The Ultimaker S3 comes in the more compact footprint of the current Ultimaker 3, packed with all of the advanced features currently found in the S5.
If you're new to Ultimaker 3D printers, they are known to be the most reliable dual extrusion printers on the market. While there are dozens of decent single extrusion printers out there that vary wildly in price and quality, there are fewer choices when it comes to reliable dual extrusion system taking advantage of soluble supports. We have found it to be one of the best choices for engineers, designers, film production and higher education with the requirement of continuous printer up-time. Sitting at a fraction of the price for industrial machines with similar (or even more limited) capabilities. Ultimaker is truly the class standard for dual extrusion, reliability and ease.
What's new with the S3 compared to the Ultimaker 3?
The S3 is packed with many key features and upgrades passed down from the S5. From a usability standpoint, you'll notice the following improvements:
- S-Series Printhead - Improved S-Series Printhead design with less chance of flooding and greatly enhanced auto-leveling.
- Large Touchscreen Interface - The intuitive straight forward interface from the S5 is now apart of the S3, making everything easier from displaying a preview of your print before printing to animated visual instructions during filament cleaning. The touchscreen has a glass surface that is easy to maintain with a high contrast LCD that reacts quickly and decisively to touch commands.
- Hardened feeder wheel - Now fully compatible with abrasive composite filaments such as carbon fiber nylon. In addition to mechanical compatibility, material settings are pre-configured by the filament manufacturer for easy software compatibility. This allows a low barrier to entry to effectively utilize industrial carbon fiber and glass fiber composite filaments. Choose the material, select the profile and you'll never worry again about tinkering with settings for each material type.
- Flow sensor - Detects abnormalities in the material flow caused by tangled filaments, end of roll and even nozzle jams. Automatically pauses your print so you can fix the issue and resume your print. This reduces the risks of lengthy prints by allowing correction of simple user errors such as loading a spool with not enough material when beginning a print.
- Internal power supply - Factory certified with cMET markings for use in Canada recognized by the CSA. The internalization of the power supply means that you have less cables and wires to contend with. A single 110v power cable from the machine to the socket makes for easier and cleaner cable management and scaling.
- New stepper drivers and motherboard - Gives a boost in print quality vs the Ultimaker 3 with a more silent operating noise floor.
- Front Glass Door - A functional safety feature that keeps a more thermally regulated printing environment.
- Backwards/Forwards Compatible UM Port - Allows for future-proofing and expansion of addons. (such as the S5 pro bundle)
- A stiffer frame and larger rods - reduces ringing artifacts and improves print quality and head stability.
- Multi-point automatic leveling - Next-generation worry-free, hands-free auto-leveling procedure with multiple point detection and mesh bed leveling. Have the confidence that the new Ultimaker S3 will auto level better than you will manually level.
These are just some of the many ways the S3 is improved over the already venerable UM3.
Is the S3 a right fit for you?
Here are the main considerations:
- Dual extrusion - By far the biggest consideration, whether it is for multi-material (such as Hard/soft combination) or water-soluble (dissolvable) supports. Ultimakers are the best dual extrusion printers on the market at this price point. Many people think Dual extrusion is for 2 different colors, but the main consideration is how well supports can be made insoluble materials, reducing manual labor for cleanup time. Improving the overhang contact surface quality as well as dimensional accuracy, and reducing the operator training requirements since you can print virtually any object with soluble supports without considering the limitations of single support printing. Read more on dual extrusion benefits here.
- Easily diversify material choices - If you need to use a variety of different types of materials such as Nylon, PLA, ABS, Carbon fiber look no further. Ultimakers, by far, have the shortest learning curve in utilizing the plethora of materials now available for FFF printing. Other printers require the operator to be somewhat familiar with each material they choose so they can select the correct temperature and feedrate settings. With the Ultimaker ecosystem, Cura has pre-installed material profiles for first and third party materials so it's as easy as picking the right material from a menu.
- Simple learning curve - Ultimaker printers rank among the easiest system to set up, learn and use. With the smallest footprint to build-size ratio of any desktop printer. Setup and operation is ranked highest in the industry. No need for hours of calibration and tinkering. From Unboxing to 24/7 part production, the workflow has been streamlined so you'll be fully up and running within a hour.
- Build Volume - The S3 build volume is a very respectable 9"x7.5"x8". If you require a larger printer, we would suggest stepping up to the S5.
- Canadian Support and Training - Ultimakers are intended to be running day and night reliability. But if something goes wrong, Shop3D offers the highest level of support for Ultimaker products as the authorized repair center for Ultimaker in Canada. We stock spare parts in our warehouses in Toronto and Vancouver that serves Canadians nation-wide. We also staff Ultimaker trained technicians who act as your direct support line. With Shop3D's exclusive bridge printing services, you can offload your production spikes to us without tying up your prototyping machine. 48 hour email ticket responses are no longer an acceptable standard.
Ultimaker S5 Pro Bundle: Enterprise focused production solution
The S5 Pro Bundle is the answer to the industry's demand for 24/7 continuous printing while maintaining the ease of use using automation to suit the rigorous demands of the professional and enterprise customer. The S5 pro bundle includes two essential components building upon the success of the S5. The Air Manager, optimizing the airflow, and filtering UFPs and the Material handling station for automatic loading of materials and humidity control.
The Air Manager addresses two main issues printing in difficult materials
- Environment management - The Air Manager covers the top of the exposed portion of the S5 creating a much more stable printing environment, preventing drafts and shop contaminants from entering the printing area. This stabilization drastically improves the performance of some materials prone to extreme warpage such as nylon and ABS.
- Controlled extraction - The material is communicated to the air manager and different airflow can be optimized for each material to optimize print quality and UFP filtering.
- Ultrafine particles (UFP) filtering- Some materials produce more toxic particles when heated to a certain printing temperature like ABS and PC, the Air Manager ensures that the environment is scrubbed clean with EPA filters Up to 95%. The Air Manager creates a negative pressure inside the machine so the air can be directed through the Air Manager.
- Connectivity - Connects to Cura and the S5, and will notify you when it needs a filter change. No separate power cord is required as it plugs directly into the S5.
Highly recommend for labs and small environments that may not have adequate ventilation and adding an extra layer of safety requirements, the Air Manager is an easy, elegant solution to solving those issues stylishly and effectively.
Installation is drop-in, and locks into place on existing S5's. Purchase the Pro bundle together to save.
Material Handling Station
The S5 material handling station automates manual low-value actions in the 3D printing processes such as loading materials, changing reels when finished, and drying the materials with prolonged moisture exposure. This automated station frees up your engineers' time for more high-value tasks. In addition, it ensures a predictable and controllable environment for the materials so the output is more consistent and not dependent on environmental factors (such as relative humidity) for hygroscopic materials.
What does this mean for you?
- Automatic loading and unloading of filaments into the S5 - If you're printing large parts, your prints could last days to even a week. With the Material Station, you don't need to worry about running out of material. Capable of loading 6 x 1kg+ rolls of material. The station will automatically switch to the next roll when the initial one is finished greatly reducing the need to keep an eye on the material usage.
- Form Factor - Front loading materials with a transparent window allows you to quickly glance at your printer and ascertain the status of your materials. Front-loading also eliminates the need for operators to reach towards the back of the machine allowing placement of the machine where the sides and back are no easily accessible. The S5 sits securely on top of the Material Station keeping the same small footprint that you're use to.
- Humidity Control - Hydroscopic materials such as Nylon and PVA can change in printability, quality and even mechanical properties over time as it naturally absorbs atmospheric moisture. The Material Station's primary function is to keep all the filaments at a humidity below 40%. Ensuring consistency in printing quality and prolonging the life of materials compared to them being stored in open air. (especially in humid provinces)
- Regenerating Desiccant Pack - The humidity control unit will turn on once a day (or more if required) to regenerate the internal desiccant pack to ensure a constant below 40% humidity. No need to replace the pack manually.
- Fully integrated into Cura and Ultimaker software ecosystem - From the communication between the S5 and the Material Station, to setting up prints in Cura, the Material Station is fully integrated into Cura. The Material Station has NFC detection, and will automatically switch to the correct spool when a print job is submitted and can feed to the extruder of your choice.
- Fully compatible with 3rd party, abrasive and composite materials - Equipped with the same hardened feeder drive wheels as the S5 and the S3, the Material Station comes fully capable of handling Carbon fiber and other abrasive materials right out of the box.

Who this is for?
From serious S5 users printing large scale models and engineers or design shops that try to run the printer 24/7. This station takes manual checks, humidity worries and filament run out out of the equation so you can spend more time filling up the print queue with designs an print jobs.
We recommend the Pro bundle and Material Station for users that:
- Use PVA and Nylon or Nylon Carbon fiber is part of your standard array of regular materials
- Want their S5 to be printing non-stop. 24/7
- Medium to High volume production or prototyping
- A studio or production environment where there are multiple engineers and designers using the S5 at once with multiple material changes.
- Print farm setups or want a cleaner printer layout
- Print with PVA and Work in a humid environment
- Service bureaus that rely on constant up-time and print-time.
We don't believe the Material Station is necessary if:
- You print mostly in PLA without supports
- The printer is used in K-12 Education
- You have sporadic need of the printer
The Material Station comes with a 1-year manufacturers warranty and is available individually or as a savings bundle with the Air Manager.
Also in News
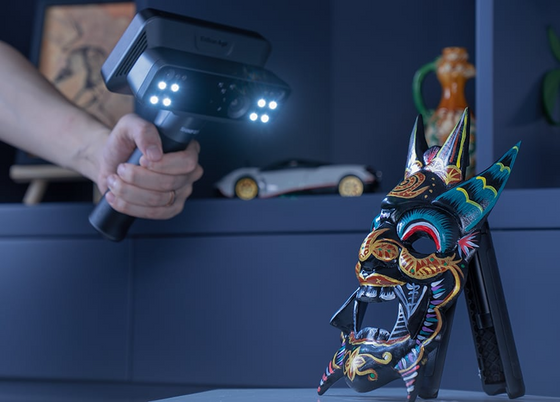
Shop3D.ca Open House: EinScan Rigil 3D Scanner - Technical Training & Demo
August 19, 2025
Join the Shop3D.ca technical team for an interactive demo of the new EinScan Rigil 3D scanner. Learn the ins and outs of professional 3D scanning, and bring a medium-sized object to scan. You’ll leave with your very own 3D model file—just make sure your item is light enough to handle and can be rotated during scanning.
![[Exclusive Webinar] Scan, Print, Maintain, Train: End-to-End Solutions with Shop3D](http://shop3d.ca/cdn/shop/articles/webinar_-_services_560x.jpg?v=1751648502)
[Exclusive Webinar] Scan, Print, Maintain, Train: End-to-End Solutions with Shop3D
July 04, 2025
Shop3D goes beyond sales and distribution of cutting-edge 3D printing equipment - we also offer a full range of end-to-end services to help you make the most of your 3D printing investment. Join our webinar on Thursday, July 17, 11am ET, to discover our range of solutions.
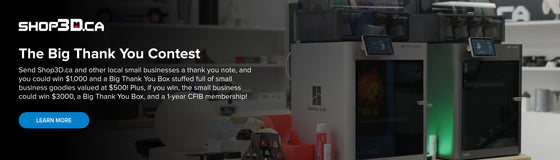
Send us a thank you for a chance to win BIG!
July 02, 2025
Send Shop3D.ca and other local small businesses a thank you note and you could win $1,000 for yourself and $3,000 for the small business you thank. Plus, you both win a Big Thank You Box stuffed full of small business goodies!