How to 3D print metal with BASF Ultrafuse 316L Stainless
November 13, 2020
A constant question we get from our clients and folks like you calling in is "plastic is great but can I 3D print metal?"
Our answer used to be "you can't really do it unless you have around $100,000 to spare" but that's behind us. BASF's Ultrafuse 316L unlocks the ability of your 3D printer to 3D print metal at home or at your business.
What we'll go through:
- Metal Workflow
- 3D Printer specifications
- Printing parameters
- Shrinkage
- Design Guidelines
- Best practices
Metal Workflow
Here's an outline of the workflow you can expect to have when dealing with this metal filament. The green part is what you 3D print, and you will then send it out to DSH in the states to carry out the post processing of your part. They will debind and sinter your parts and provide a full report so you can learn and improve for your next run.

3D Printer specifications
Below you can review the basic requirements for your 3D printer, in today's market, most 3D printers meet or exceed these specs. Keep in mind that a hardened nozzle is a must, hardened feeder gears are recommended.

Printing Parameters
Next up are the printing parameters. If you have the Ultimaker S3 or S5, you can get the printing profile directly on the marketplace, otherwise follow these guidelines:

Shrinkage
You'll need to scale your part to account for the shrinkage during debinding and sintering. That can be done in CAD, Meshmixer, or even your slicer.
Make sure you uncheck "Uniform Scaling" when doing this. You will need to scale your parts 120% in the X and Y direction and 126% in the Z direction.
Cura

PrusaSlicer

Design Guidelines
It's important to keep in mind the following design guidelines for your metal parts. Following these will increase the success of 3D printing, debinding and sintering all together. Having said that, we sometimes slightly deviate from these suggestions. Experiment but keep it within reason!
Best Practices
There are a few things you want to keep in mind when printing with Ultrafuse 316L.
- Start small and make sure that your printing parameters are good. The cost of failure is bigger due to the cost of the filament
- Avoid printing parts that require supports. If you must, use supports when the features exceed 45 degrees
- Tune your first layer to perfection, too high and the print will not stick, and too low will make it harder to remove after or even clog your nozzle.
- Clean up your part as much as you can after printing. You can remove stringing, and even use sand paper to smooth out the surface.
- For critical features, you will be able to bring them to size once you get your parts through traditional machining methods (milling, turning, surfacing, grinding, tumbling, etc)
Next Steps
If you made it to the end, you are probably looking to get your hands on some of this Ultrafuse 316L filament. You can go on this page to get a spool in either Ø1.75mm or Ø2.85mm
If you have more questions, want to talk about your application or wanted to do this as a print service. Reach out to our team through phone, chat or email. We are always happy to help you!
Also in News
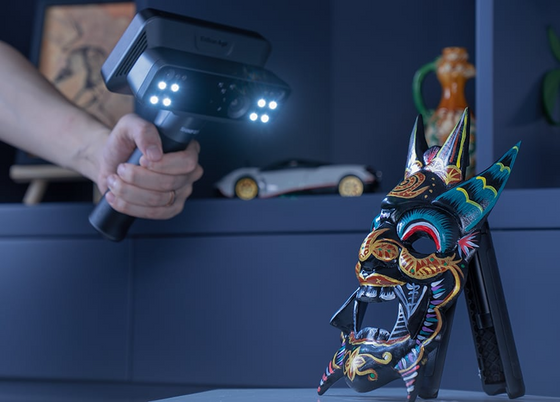
Shop3D.ca Open House: EinScan Rigil 3D Scanner - Technical Training & Demo
August 19, 2025
Join the Shop3D.ca technical team for an interactive demo of the new EinScan Rigil 3D scanner. Learn the ins and outs of professional 3D scanning, and bring a medium-sized object to scan. You’ll leave with your very own 3D model file—just make sure your item is light enough to handle and can be rotated during scanning.
![[Exclusive Webinar] Scan, Print, Maintain, Train: End-to-End Solutions with Shop3D](http://shop3d.ca/cdn/shop/articles/webinar_-_services_560x.jpg?v=1751648502)
[Exclusive Webinar] Scan, Print, Maintain, Train: End-to-End Solutions with Shop3D
July 04, 2025
Shop3D goes beyond sales and distribution of cutting-edge 3D printing equipment - we also offer a full range of end-to-end services to help you make the most of your 3D printing investment. Join our webinar on Thursday, July 17, 11am ET, to discover our range of solutions.
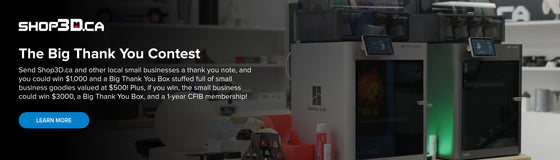
Send us a thank you for a chance to win BIG!
July 02, 2025
Send Shop3D.ca and other local small businesses a thank you note and you could win $1,000 for yourself and $3,000 for the small business you thank. Plus, you both win a Big Thank You Box stuffed full of small business goodies!