Creating Product Casings with the Mayku FormBox
June 24, 2022
In this article, we’ll show you how a 3D printer can be twinned with a Mayku FormBox to speed up and improve the manufacture of product casings for a working electronic product. In short, using a 3D printer for the creation of templates (rather than printing the product casings themselves) will enable the FormBox to rapidly manufacture the parts themselves.
Before showing this in practice, an object was needed to serve as an example. Predictably, somebody suggested a toy for their cat, and everybody decided the idea simply couldn’t be improved upon. Read on to find out how a vacuum former enabled rapid production of the Lazer Chazer.
Introducing… THE LAZER CHAZER
Essentially, the Lazer Chazer is an open-source laser toy for cats. It’s an easily-assembled box that houses a laser. This laser projects onto walls and floors, giving your cat something to chase after whilst you take videos of it. We love it.
The primary problem with producing the Lazer Chazer is that the reliance on 3D printed parts creates long lead times as you wait for your parts to print. Additionally, the limitations of 3D printing materials means that the design has to be adapted (like through the addition of the window) to work. It’s also currently impossible to 3D print totally transparent parts, but very easy to form a transparent part from a 3D print using a FormBox.
Speeding up production
To be clear, if you’re just producing one Lazer Chazer, then 3D printing and vacuum forming are going to take roughly the same amount of time. However, as soon as you expand your production run to 2 units, or decide you want to experiment or iterate, vacuum forming becomes a significantly better option.
On average, the Lazer Chazer takes just over 6 hours to 3D print with average settings of 0.2mm layer height, 0.8 mm wall thickness, and 10% infill. Switch to a vacuum former, however, and the manufacture time drops below 5 minutes once you have your templates. With a fairly small run of 10 units, 3D printing the Lazer Chazer becomes a long, arduous and potentially expensive process.
Vacuum forming the same run of 10 products is 661% faster. Adapting a 3D print design to accommodate the FormBox is often the best alternative to investing thousands in a print farm.
Upgrading the design
Another problem with 3D printing the Lazer Chazer is that you cannot create a transparent area for the laser to project through. As a workaround, the open source design comes with a small window.
In order to improve the design, we used transparent materials to remove the need for a window. Fortunately, the range of plastics that you can use while vacuum forming made this simple. Without the need for a window our product is more durable, safer, and less likely to be destroyed through accidental damage.
Beyond the specific example of the Lazer Chazer, working with vacuum forming enables you to work with a variety of textures and finishes. For instance, if you wanted to create a Lazer Chazer with a sandy texture, you could easily do so by applying sand to your template.
Decreasing the cost of production
Beyond delivering speed and unlocking superior designs, producing runs of the Lazer Chazer was also far more affordable when using the FormBox. When printed with a spool of good quality PLA, the cost per case came out at $2.39. In comparison, the FormBox created casings cost $1.47. Even if you factor in the cost of the 3D printed templates, the casings for a run of 10 units is 23% cheaper when vacuum formed.
Just remember to print your templates in a heat resistant material, such as ABS.
Adapting to new technologies
Recognizing the right role for a manufacturing technology to play in the production of your product casings can have a massive impact on speed, cost, and quality. Whilst the Lazer Chazer was collaboratively developed as a 3D printing project, smart use of the FormBox enabled significant savings of both time and money once production passed a single unit. Furthermore, unlocking the ability to easily produce transparent parts and play with textures enables those with a FormBox to enhance and progress the Lazer Chazer’s design.
Also in News
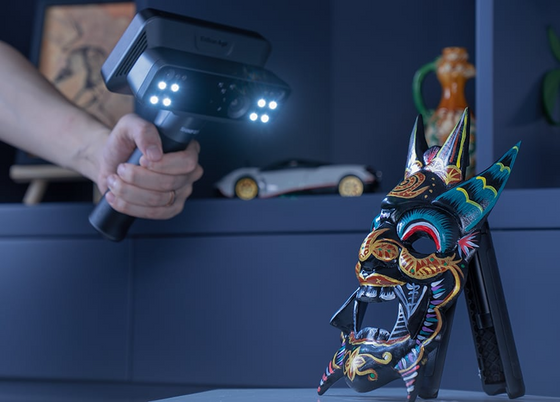
Shop3D.ca Open House: EinScan Rigil 3D Scanner - Technical Training & Demo
August 19, 2025
Join the Shop3D.ca technical team for an interactive demo of the new EinScan Rigil 3D scanner. Learn the ins and outs of professional 3D scanning, and bring a medium-sized object to scan. You’ll leave with your very own 3D model file—just make sure your item is light enough to handle and can be rotated during scanning.
![[Exclusive Webinar] Scan, Print, Maintain, Train: End-to-End Solutions with Shop3D](http://shop3d.ca/cdn/shop/articles/webinar_-_services_560x.jpg?v=1751648502)
[Exclusive Webinar] Scan, Print, Maintain, Train: End-to-End Solutions with Shop3D
July 04, 2025
Shop3D goes beyond sales and distribution of cutting-edge 3D printing equipment - we also offer a full range of end-to-end services to help you make the most of your 3D printing investment. Join our webinar on Thursday, July 17, 11am ET, to discover our range of solutions.
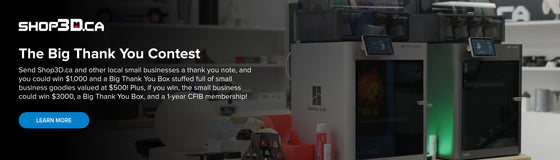
Send us a thank you for a chance to win BIG!
July 02, 2025
Send Shop3D.ca and other local small businesses a thank you note and you could win $1,000 for yourself and $3,000 for the small business you thank. Plus, you both win a Big Thank You Box stuffed full of small business goodies!