Gillette Uses 3D Printing to Unlock Consumer Personalization
October 24, 2018
New technologies create opportunities for businesses to evolve and re-think their business models. Additive manufacturing is one such technology. 3D Printing offers advancements in prototyping and has grown to allow the creation of end-use parts. Where 3D printing excels is ease of customization, and razor manufacturer Gillette is taking full advantage of that with their new Razor Maker™ concept.
However, this level of customization required Gillette to re-think their approach to manufacturing. Previously, 3D printing was only used for prototyping designs but advancements with the material and hardware have made it viable for producing end-use parts. Cue the Formlabs Form 2. After a razor handle is designed on the website by the consumer, this stereolithography (SLA) printer allows for it to be grouped with other designs and printed in a single batch. Each handle is then washed, post-cured, coated and assembled before being shipped directly to the consumer.
Also in News
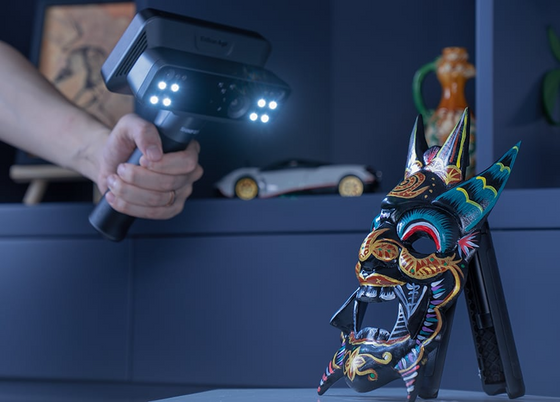
Shop3D.ca Open House: EinScan Rigil 3D Scanner - Technical Training & Demo
August 19, 2025
Join the Shop3D.ca technical team for an interactive demo of the new EinScan Rigil 3D scanner. Learn the ins and outs of professional 3D scanning, and bring a medium-sized object to scan. You’ll leave with your very own 3D model file—just make sure your item is light enough to handle and can be rotated during scanning.
![[Exclusive Webinar] Scan, Print, Maintain, Train: End-to-End Solutions with Shop3D](http://shop3d.ca/cdn/shop/articles/webinar_-_services_560x.jpg?v=1751648502)
[Exclusive Webinar] Scan, Print, Maintain, Train: End-to-End Solutions with Shop3D
July 04, 2025
Shop3D goes beyond sales and distribution of cutting-edge 3D printing equipment - we also offer a full range of end-to-end services to help you make the most of your 3D printing investment. Join our webinar on Thursday, July 17, 11am ET, to discover our range of solutions.
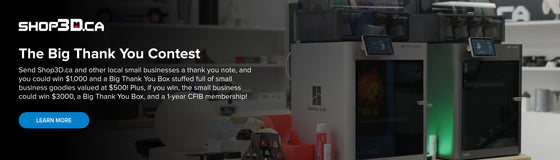
Send us a thank you for a chance to win BIG!
July 02, 2025
Send Shop3D.ca and other local small businesses a thank you note and you could win $1,000 for yourself and $3,000 for the small business you thank. Plus, you both win a Big Thank You Box stuffed full of small business goodies!