3D Printing Metal Parts: Methods and Cost
June 11, 2020
This educational post will summarize the different options and manufacturing methods available for metal 3D printing. We'll cover the in-house and outsourcing costs and why BASF's Ultrafuse 316L is the best way to enter the metal 3D printing space.
Overview:
- The different options for metal 3D printing
- The cost of bringing metal additive manufacturing (AM) in-house
- The cost of outsourcing metal additive manufacturing (AM)
- Direct comparison between in-house and outsourcing
- The basics of SLM and DMLS
Metal Additive Manufacturing Methods
There are three major methods for manufacturing 3D printed metal parts: Selective Laser Melting (SLM), Direct Metal Laser Sintering (DMLS) and Fused Filament Fabrication (FFF) using metal filaments.
Selective Laser Melting (SLM) and Direct Metal Laser Sintering (DMLS) are the traditional ways to 3D print metal parts. These two methods are out of reach for many individuals and companies because the costs are quite high. If you wanted to run a single part you are looking at a starting cost of around $500 USD. If you wanted to purchase an entire system, you are looking at approximately $1,000,000 USD and the specialized metal powders can cost about $400 USD per kilogram.
In recent years, a few companies introduced complete desktop and studio metal printing systems for around $100,000 - $150,000, which include a 3D printer, a debinding station, and a sintering station. Part costs have also decreased.
FFF 3D printers, have become a crucial tool for many businesses, and universities as costs decrease while quality and reliability increase. It is an additive manufacturing technique that is adopted by makers and large corporations alike. Until today, the only materials you could 3D print at home or the office were different kinds of polymers like ABS, Nylon, and PLA. Enter BASF's Ultrafuse 316L Stainless Steel filament. Yes, you read that right, it's a metal filament that can be extruded on almost any consumer 3D printer. Once the part is printed, it is sent out for debinding and sintering and what you get back is a complete stainless part; ready for use or further machining/finishing.
Metal Additive Manufacturing: How Much It Costs
We covered the different ways to 3D print and now see what these various methods cost. Let's take a fairly sophisticated tool like this bottom bracket installation tool for bicycles:
This part is relatively difficult to machine and requires a few different setups with some specialized tools. It seems like an excellent example of why you might want to use a metal 3D printer.
In-House Manufacturing - Metal 3D Printed Parts
Capital investment | Material cost | Debinding/sintering cost | Post-processing steps | Support material type | Materials that can be used on the machine | |
SLM / DMLS | ~ $500,000 - $1,000,000 USD | ~ USD 56, based on $400 / kilo powder cost and weight of 140 grams | NA, consider electricity costs, gas cost, etc. | Machining, cutting, EDM | Same material supports, metal supporting metal |
Metal only Different types of metal powders |
Metal Desktop 3D Printers | ~ $130,000 USD | ~ USD 20 | NA, consider debinder and furnace running cost | The 3D printed part must go through debinding and sintering | Cermaic release layers allow to break away support material |
Metal only Different types of metal filaments/rods |
Ultimaker S3 / S5 | ~ $5,000 - $13,000 CAD | ~ CAD 32 | ~ USD 14 or roughly USD 100 per kilogram | The 3D printed part must be sent out for debinding and sintering | No supports or same material supports, metal supporting metal |
Metal: BASF 316L Polymers: ABS, PA, PAHTCF15, PET, etc. |
* All information except the Ultimaker row is to be taken with a grain of salt, as the figures are based on limited available information.
As you can see from this table, up until now with the introduction of Ultrafuse 316L, the barrier of entry for metal 3D printing was quite high at over USD 100,000. BASF's 316L can be printed on any compatible desktop 3D printer making it easy to adopt and affordable to use.
Outsourcing Manufacturing - Metal 3D Printed Parts
Manufacturing Method | Material | A single part ($CAD) | Average cost for ten parts converted to CAD |
DMLS | 316L Stainless Steel | ~ $950 *3D Hubs | ~ $225 per part *3D Hubs |
FFF (Ultimaker style machine) | Ultrafuse 316L (Stainless Steel) | ~ $100 *Sculpteo | ~ $95 per part *Sculpteo |
Metal Desktop 3D Printers | NA | NA | NA |
CNC Machining | 316L Stainless Steel | ~ $550 *3D Hubs | ~ $160 per part *3D Hubs |
* These are estimates taken directly from the instant quotation tools
Even when outsourcing to use someone else's desktop 3D printing machine and using 316L, we can still see a significant cost decrease when using BASF's new Ultrafuse filament.
In-House versus Outsourcing Manufacturing: Metal 3D Printed Parts
Manufacturing Method | In-house - part cost | Outsource - part cost (average over ten parts) |
DMLS | ~ CAD 80 (material cost only) | ~ $225 per part |
FFF (Ultimaker style machine) | ~ CAD 06 (material + post-processing cost) | ~ $95 per part |
CNC Machining | NA | ~ $160 per part |
Metal Desktop 3D Printers | ~ CAD 30 (material cost only) | NA |
So what's the conclusion here? What should you get, if anything, and why?
If you already have a 3D printer, all you need is an abrasive nozzle and some of the BASF 316L filament, and you can start 3D printing metal parts today. It's as simple as that.
If you don't have a 3D printer, and you're looking at 3D printing metal parts, you should look into getting a desktop 3D printer first. Imagine spending all this money to 3D print a metal part, in-house or not, only to realize you forgot to put a fillet or relief somewhere, and now your piece doesn't fit. A desktop 3D printer allows you to test your parts with inexpensive polymers like ABS and Nylon for fit and function and move on to metal if needed. It is also a great way to understand the strengths and limitations of the additive manufacturing process so that you can design for manufacturing just like you would for machining or injection moulding.
So when should I get into the $100K+ metal 3D printers?
The metal options for desktop 3D printers are currently limited to the Ultrafuse 316L filament, but we are sure that there will be more metal filaments available in the future. If Ultrafuse 316L is not enough to satisfy your needs, explore the higher-end metal dedicated systems that offer complete in-house solutions and more material choices.
Consider these printers if you have proven applications and can see using metal additive manufacturing regularly. Again, a great way to introduce metal AM is by getting a professional desktop machine like the Ultimaker S3 or Ultimaker S5, allowing you to explore both polymers and metal at the same time.
The basics of SLM and DMLS
Both SLM and DMLS use a laser and specific metal powders to create metal parts. Often these systems are expensive and require dedicated rooms or self-contained systems due to the inert gases present like Argon that minimize oxidation of the metal powder.
The main difference between SLM, Selective Laser Melting and DMLS, Direct Metal Laser Sintering is the process in which the powder becomes metal.
SLM utilizes a powerful laser, sometimes up to a Kilowatt of power, to bring the metal powder into a molten state so that it bonds to the previous layer. This method often introduces heat-related stresses to the parts, and heat treating is required to alleviate those stresses.
DMLS still utilizes a laser to create metal parts, but instead of melting the powder, the laser heats it enough to bond or sinter to the previous layer. Unlike SLM, there are minimal heat stresses and requires no heat treatment of the part after the fact.
In both of these methods, the parts bond to a metal build platform and use same-material supports. This requires the use of specialized operations like cutting, machining and wire cutting (EDM) to remove supports and remove the part from the platform.
Further suggested readings:
Also in News
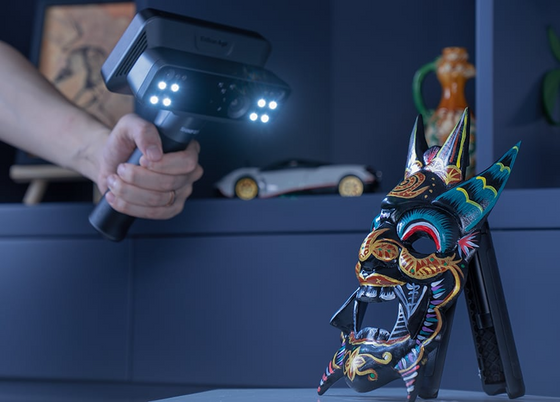
Shop3D.ca Open House: EinScan Rigil 3D Scanner - Technical Training & Demo
August 19, 2025
Join the Shop3D.ca technical team for an interactive demo of the new EinScan Rigil 3D scanner. Learn the ins and outs of professional 3D scanning, and bring a medium-sized object to scan. You’ll leave with your very own 3D model file—just make sure your item is light enough to handle and can be rotated during scanning.
![[Exclusive Webinar] Scan, Print, Maintain, Train: End-to-End Solutions with Shop3D](http://shop3d.ca/cdn/shop/articles/webinar_-_services_560x.jpg?v=1751648502)
[Exclusive Webinar] Scan, Print, Maintain, Train: End-to-End Solutions with Shop3D
July 04, 2025
Shop3D goes beyond sales and distribution of cutting-edge 3D printing equipment - we also offer a full range of end-to-end services to help you make the most of your 3D printing investment. Join our webinar on Thursday, July 17, 11am ET, to discover our range of solutions.
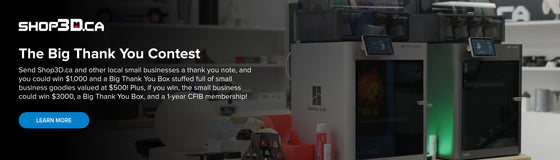
Send us a thank you for a chance to win BIG!
July 02, 2025
Send Shop3D.ca and other local small businesses a thank you note and you could win $1,000 for yourself and $3,000 for the small business you thank. Plus, you both win a Big Thank You Box stuffed full of small business goodies!