Best Practices For 3D Printing Jewelry
November 10, 2022
3D printing is changing the way we make things. From toys to furniture, 3D printers are opening up a world of possibilities for designers, engineers and consumers alike. With 3D printing, jewelry designers are able to produce designs that would be incredibly difficult to hand carve in the traditional manner. Breakthroughs in castable resins are setting new standards for the quality available through an affordable desktop 3D printer. Here are a few tips and tricks to achieve the best results when printing jewelry:
Making your Feed Sprues in CAD

Design With Polishing Loss In Mind

During the polishing stage there will be a material loss of around 0.2mm all around your model. For example, if you need your ring shank to measure 1.6mm finished, you will have to design and print the ring shank at 1.8mm taking into account it will be polished down to 1.6mm. It is key to focus on the thickness of the entire design to ensure it doesn’t go below the printer’s layer height capabilities.
Ensure You Have A Watertight Model
It is important to build and boolean your model properly to have the best results and increase your casting success rate. This means having a watertight design which implies that there are no holes or non-manifold edges in your model. Using a design that is not properly built or repaired may lead to printing issues as well as casting issues.

3D Printing Jewelry Workflow
Also in News
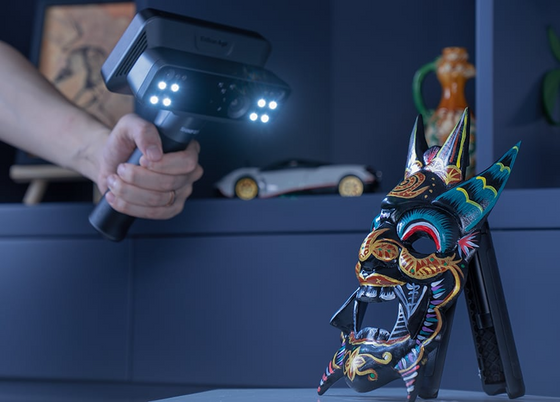
Shop3D.ca Open House: EinScan Rigil 3D Scanner - Technical Training & Demo
August 19, 2025
Join the Shop3D.ca technical team for an interactive demo of the new EinScan Rigil 3D scanner. Learn the ins and outs of professional 3D scanning, and bring a medium-sized object to scan. You’ll leave with your very own 3D model file—just make sure your item is light enough to handle and can be rotated during scanning.
![[Exclusive Webinar] Scan, Print, Maintain, Train: End-to-End Solutions with Shop3D](http://shop3d.ca/cdn/shop/articles/webinar_-_services_560x.jpg?v=1751648502)
[Exclusive Webinar] Scan, Print, Maintain, Train: End-to-End Solutions with Shop3D
July 04, 2025
Shop3D goes beyond sales and distribution of cutting-edge 3D printing equipment - we also offer a full range of end-to-end services to help you make the most of your 3D printing investment. Join our webinar on Thursday, July 17, 11am ET, to discover our range of solutions.
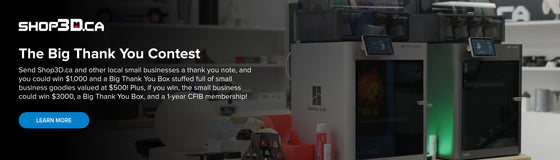
Send us a thank you for a chance to win BIG!
July 02, 2025
Send Shop3D.ca and other local small businesses a thank you note and you could win $1,000 for yourself and $3,000 for the small business you thank. Plus, you both win a Big Thank You Box stuffed full of small business goodies!