Electroplating on 3D Prints
October 20, 2021
Get the benefits of metal on a plastic 3D print with electroplating. While metal 3D printers and metal filament are excellent options for metal parts, sometimes you only need the look of metal to prove your concept or to add magnetic or conductive properties. In these cases, electroplating is a simple and lower cost alternative to making a full metal part and can work with the 3D printer that you already own.
What Is Electroplating?
Electroplating is the process of using electrodeposition to coat an object in a layer of metal(s). Engineers use controlled electrolysis to transfer the desired metal coating from an anode (a part containing the metal that will be used as the plating) to a cathode (the part to be plated). We decided to put this process to the test by electroplating some of our 3D prints. Read on to see how we did it and what we learned!
Why Electroplate a 3D Print?
Electroplating provides a plastic 3D print with a metal coating allowing it to gain the properties of the metal it is coated in. This is great for giving plastic prints the appearance of metal but can also add properties such as conductivity or magnetism. Some of the other reasons to electroplate include:
- Ability to create high quality conductive parts
- Gives parts a metal finish without needing to actually print in metal
- Increases part strength and durability
- Improves part resistance to environmental factors (i.e. chemical exposure, UV light)
- Preserves natural elements that are prone to decay
- Ability to prototype parts in metal before committing to full production runs
Professional Electroplating vs DIY Electroplating
On the surface, electroplating sounds like something you need to have professionally done. However DIY kits are available so the hobbyist could electroplate at home. We wanted to see how viable these DIY kits are and if they make sense for our customers.
In the image below, you will find examples of parts which have been electroplated professionally and some done via the DIY Method. Can you guess which is which?

All the skulls were 3D printed with the DIY method at Shop3D, while the cube was done professionally offsite!
Below you will find a comprehensive comparison listing the pros/cons of both the DIY and Professional methods of electroplating:
Professional Electroplating
Professional electroplating involves sending your parts to a third party service to plate your parts.
Pros:- Consistent Results
DIY is great for experimenting but the experienced staff and industrial setups at a service bureau are invaluable when you want reliable and consistent results or ensure that critical dimensions are maintained.
-Amazing finish
When compared with the results of our DIY method (read on below) it’s clear that the professionally electroplated part has a thicker and more even coat of material.
- Wider selection of plating material
From what we saw, DIY kits are more limited in materials while professional electroplating options include Palladium, Rhodium, Ruthenium and alloys for more specific applications.
- Large Scale Batch Production
Our DIY kit was great for single parts, but wasn’t optimized for larger volumes. We also found our results were inconsistent between pieces. If you’re looking to do a large scale batch then we recommend going the professional route.
- Metallic Shine
Our professionally plated Formlabs parts came polished with a great metallic shine. We attempted to polish our DIY parts but in some cases it removed the plating.
- Expensive when compared to DIY options
- Long turnaround time
DIY Electroplating
- Pros- Cost effective alternative
We got started with a $65 CAD electroplating kit, but there may be even more savings if you create the solutions yourself. Compared to the average cost for Professional electroplating, you’re looking at savings on your parts.
- Short turnaround time
No shipping or transferring of parts involved, you can set up the DIY kit anywhere in your house and start electroplating. We saw results in as little as 1 hour. However the longer we ran the current, the better the results.
- Perfect for a single part or for a project
- Whether you are teaching your students or creating a single part, this is an easy project for the DIYer to take on.
Cons:- More effort to get a quality finish
- Getting a good finish took some experimentation. We had some issues with current lines appearing on our piece when the anode and cathode were too close together and it took a few tries to get a coat thick enough to polish.
- Finished shine depends on materials and levels of after care.
- Prepping the surface before electroplating is crucial for getting a good finish, but with the DIY methods there was the added challenge of getting a thick coat and polishing it to a shine. We found some of our materials oxidized, changing the look from when it was pulled out of the solution.
Which technology makes the most sense for you? We picked up a simple electroplating kit and tested it out so we can share the experience and answer your questions.Preparing 3D Prints for DIY Electroplating
To prepare a 3D print for electroplating the plastic has to be coated with a conductive material. This can be achieved with either a metal paint or spray. For our project, each print was sprayed in Super Shield Nickel Conductive Coating. We found this coating to adhere well to the base print, including a partial coating where we used tape to mask off one side.
While we didn’t do this for our project we highly recommend finishing your print so that it has a smooth surface, as any imperfections will be visible through the electroplating later. With SLS and FDM prints this may include filling and sanding, and SLS prints work best after beadblasting.
DIY Electroplating Methods
The Method of electroplating we used in this experiment was the “dip method”. This method calls for the object to be submerged in solution in order for the object to coat evenly. You then need to add a positive electric current via a wand into the solution and clip the negative current onto your object. The longer you have your part submerged, the better your results will be. This method was used on parts printed in FDM, SLA, SLS and 316L.
The alternative to this method is called the “swab method”. The swab method involves swabbing the selected part with the metal solution while it is connected to the anode. This method is slower, but allows for better plating in select areas. This method is ideal if you only want to plate certain parts of your print.
In order to maintain consistency, the dip method was used on all of our prints with the only variable being the amount of time that each print was submerged for.
The Results
The results of this project were generally good; We successfully plated many different 3d printing materials in copper and silver. You can read how each material reacted to electroplating below.
SLAOur SLA skull was 3D printed on the Formlabs Form 3 in Clear Resin. It was sprayed with nickel and plated in copper followed by silver. It resulted in a good coat, but developed some bubbles on the surface layer of the print. This may have been because the solution was not in motion and it created a “burn spot”.
Plating time: 2 Hours Copper, 2 Hours Silver
Our SLS skull was printed on the Formlabs Fuse 1 in Nylon 12 with a beadblasted finish. It was sprayed with nickel and plated in copper followed by silver. This was our shortest plate time at around 30 minutes per solution. The plating was decent but some areas did not get plated with the silver, resulting in a spotty finish. This is likely due to the flow of the current and may be remedied with a larger tank but could also be fixed up by using the swab method of plating to reach detailed areas.
Plating time: 30 minutes copper, 30 minutes silver
Our FDM skull was printed on an Ultimaker S5 in black filament. This was our longest plate time and was sprayed with nickel and plated with copper. The long plating time worked to produce a thicker layer that could handle buffing, as well as a fully coated piece. With some buffing you could add a shiny finish to the piece, although layer lines made it difficult to get a consistently smooth piece. The copper material oxidized and became darker over time, a sealing coat could be used to prevent this.
Plating time: 24 Hours Copper
We wanted to test out if the Ultrafuse 316L Stainless Steel filament is conductive enough to plate without going through the sintering process. To test this, half the print was sprayed with nickel by using tape as a masking layer. The entire piece was submerged for dip electroplating but the copper plating only took on the nickel coated side. Due to the proximity of the cathode to the anode, there were some lines that formed along the copper plated side of the 316L print. To avoid this pattern we suggest a larger tank.
Plating time: 8 hours Copper
Final Thoughts
Overall DIY electroplating was successful in that we can apply copper and silver plating to a number of different materials when 3D Printing by using a conductive coating. Electroplating is a great way to give a part a metallic appearance or conductive properties without the costs of metal printing. However, the DIY kits are not ideal for getting the shine or thicker coatings that can be achieved with professional electroplating services.
We recommend DIY kits for teachers, hobbyists and businesses on a budget who have the time to experiment. We recommend professional electroplating for those looking for consistent results, mass production of parts and/or materials that aren’t available through DIY or plug-n-plate kits.
Wondering if electroplating is right for your application? Contact us, and a shop3D expert will help find the right fit for your needs.
Also in News
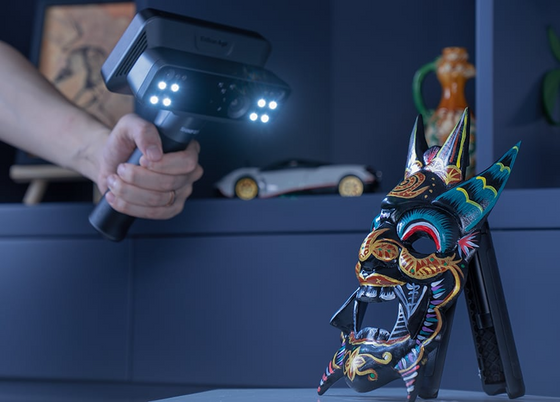
Shop3D.ca Open House: EinScan Rigil 3D Scanner - Technical Training & Demo
August 19, 2025
Join the Shop3D.ca technical team for an interactive demo of the new EinScan Rigil 3D scanner. Learn the ins and outs of professional 3D scanning, and bring a medium-sized object to scan. You’ll leave with your very own 3D model file—just make sure your item is light enough to handle and can be rotated during scanning.
![[Exclusive Webinar] Scan, Print, Maintain, Train: End-to-End Solutions with Shop3D](http://shop3d.ca/cdn/shop/articles/webinar_-_services_560x.jpg?v=1751648502)
[Exclusive Webinar] Scan, Print, Maintain, Train: End-to-End Solutions with Shop3D
July 04, 2025
Shop3D goes beyond sales and distribution of cutting-edge 3D printing equipment - we also offer a full range of end-to-end services to help you make the most of your 3D printing investment. Join our webinar on Thursday, July 17, 11am ET, to discover our range of solutions.
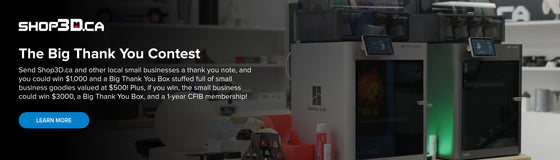
Send us a thank you for a chance to win BIG!
July 02, 2025
Send Shop3D.ca and other local small businesses a thank you note and you could win $1,000 for yourself and $3,000 for the small business you thank. Plus, you both win a Big Thank You Box stuffed full of small business goodies!