Why Dual Extrusion Matters
February 28, 2019
We've all seen and heard the hype about dual extrusion printers. But what does this actually mean for your projects? Is it worth it for your application? Is it a truly functional advantage or simply just a gimmick?
Let's have that conversation about dual extrusion in 3D printing and why this is such an important defining characteristic of modern-day 3D printers. We love our dual extrusion printers here at Shop3D and here are the main reasons why someone would want to choose a dual extrusion FFF printer for their needs:
Dual Colour Printing
The simultaneous use of two filaments on a singular print makes you question how the iconic monochrome prints we used to know have evolved. Clean no-bleeding colours give your print the polished look that better mimics that of a finished product, adding authenticity to your prototype. It also allows for clearer inset text or customized highlighting so you can bring attention to the parts with colour and localized contrast.
Multi-Material Prints
With dual extrusion, you can create parts from two different materials, which allows you to incorporate the benefits and properties of both. For example, a medical anatomical model of a hand could be printed with a stiff structural filament used to represent bone and a flexible or soft filament to mimic tendon or tissue. By mixing hard and soft materials, or elastic and stiff, this opens up what you can do with tactile feel in your prints as well as living hinges and joints. Not all materials are able to adhere to one another. Make sure to reference the material's compatibility chart before printing.
Reduce Support Removal for Complex Geometry Prints
Fused Filament Fabrication (FFF) 3D printers work by depositing melted plastic, building up a shape layer by layer. Complex shapes, extreme overhangs and bridges cause issues because the filament doesn't have a base to be deposited on. This is where supports come in.
Supports are structures printed alongside the model, creating a base to support overhangs and bridges. They can be modeled into the design or generated by the slicing program. With single-extrusion printing, the supports are printed with the same material. These can be difficult to remove and may cause cosmetic blemishes or take chunks out of the print since materials generally have great adhesion to themselves.
Dual extrusion introduces the capability of using specialty support materials as your second filament choice. These materials allow for easy-to-remove supports to make cleanup easier. Ultimaker Breakaway is a support material made to be easy to remove by pulling it off the print after printing. There are also dissolvable supports like PVA (Poly-Vinyl Alcohol) that is water soluble or HIPS (High Impact Polystyrene) which adheres to ABS and dissolves in d-Limonene.
Support Materials & Uses
- Use a PVA raft or base to print objects that don’t have a smooth flat surface with ease
- PVA is great for intricate support for complex prints since it will simply be dissolved in water in its post-processing stage
- Breakaway requires no dissolving time so it is ideal for prints where the support can be easily accessed to be removed by pliers
- Interface support allows minimal use of PVA supports since only the interface (touching layer between the support and build material) is using the PVA material which is generally more expensive.
- Same Material Supports for the most economical builds that don’t require a smooth support removed surface (increases print speed)
Multi-Part Prints
PVA can be used for more than just support, it also works to fill tolerance joints. It dissolves away to leave a tolerance between different parts.
You can also print multiple parts encased in PVA to increase print efficiency. No need to self-orient complex inter-joining parts one at a time. Print the whole stack and dissolve in water to ensure all parts are printed at once.
Dual extrusion is available on the Ultimaker 3 family, Ultimaker S5, BCN3D Sigma R19 and the upcoming Makerbot Method. Unsure if dual extrusion is right for your business? Contact us and we'll help determine the best choice for your needs.
Also in News
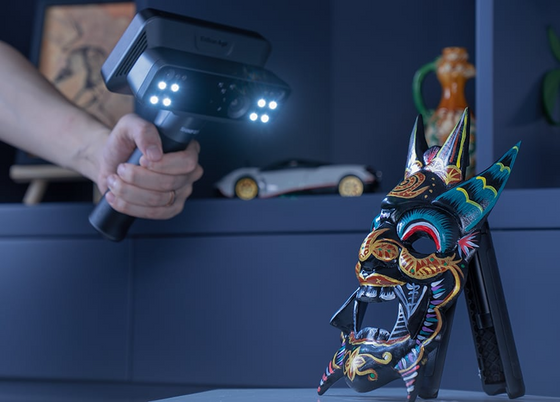
Shop3D.ca Open House: EinScan Rigil 3D Scanner - Technical Training & Demo
August 19, 2025
Join the Shop3D.ca technical team for an interactive demo of the new EinScan Rigil 3D scanner. Learn the ins and outs of professional 3D scanning, and bring a medium-sized object to scan. You’ll leave with your very own 3D model file—just make sure your item is light enough to handle and can be rotated during scanning.
![[Exclusive Webinar] Scan, Print, Maintain, Train: End-to-End Solutions with Shop3D](http://shop3d.ca/cdn/shop/articles/webinar_-_services_560x.jpg?v=1751648502)
[Exclusive Webinar] Scan, Print, Maintain, Train: End-to-End Solutions with Shop3D
July 04, 2025
Shop3D goes beyond sales and distribution of cutting-edge 3D printing equipment - we also offer a full range of end-to-end services to help you make the most of your 3D printing investment. Join our webinar on Thursday, July 17, 11am ET, to discover our range of solutions.
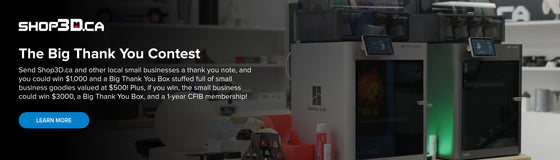
Send us a thank you for a chance to win BIG!
July 02, 2025
Send Shop3D.ca and other local small businesses a thank you note and you could win $1,000 for yourself and $3,000 for the small business you thank. Plus, you both win a Big Thank You Box stuffed full of small business goodies!