Adding 3D Printing to the Machine Shop: Lessons From A&M Tool
November 08, 2018
A&M Tool and Design started in 1948 as a family owned, single source, machine shop in Southbridge, Massachusetts. Today it still holds onto its history as a close-knit shop with talented engineers and machinists while updating their tools and facilities to remain on the cutting edge of capabilities and efficiency. This merger of modernized new equipment and reliable traditional tech gives them their industry-leading reputation as they make parts and custom machines for aerospace, optics, and robotics for customers such as Boston Dynamics, LinkNYC, NASA, Goodrich, and Corning.
Speed is the key to success in a production environment and A&M Tool is always searching for tech that can reliably and cost-effectively scale. Less than a year ago, they added the Formlabs Form 2 to their toolset. This industrial-grade Stereolithography (SLA) 3D printer allows them to create complex geometries not suitable for CNC machines, expedite prototyping workflows and increase capacity for affordably producing parts in-house. It gives the shop a real advantage. However, they are constantly finding opportunities to use 3D printed parts to enhance workflows and projects by accelerating timelines, mitigating errors and creating functional end-use parts.
Accelerate Timelines
Using the 3D printer is a material based decision. Does it need to be metal or can a polymer-based material be a substitute? When 3D printing fits the function of the piece it allows the team to make parts faster. They aren't waiting for a person to run it on a machine and they can utilize all hours; They can run a print overnight and collect it in the morning.
Communication
A&M Tool's team of talented machinists and welders are able to turn complex drawings and numerous call-outs into physical models. However, sometimes clarity is needed, especially for complex geometries like undercuts. With the availability of 3D printing, assembly or SolidWorks files can be scaled down and printed for reference. And the machinists have adopted this process and request the models themselves.
Functional End-Use Parts
The form 2 can also produce functional parts needed in a pinch. When a spider coupling for one of their large lens polishing machines arrived in the wrong size two days before a trade show they were able to quickly design and 3D print a replacement in durable resin. This printed coupling was then used to drive a two-horsepower motor on a grinding machine.
Also in News
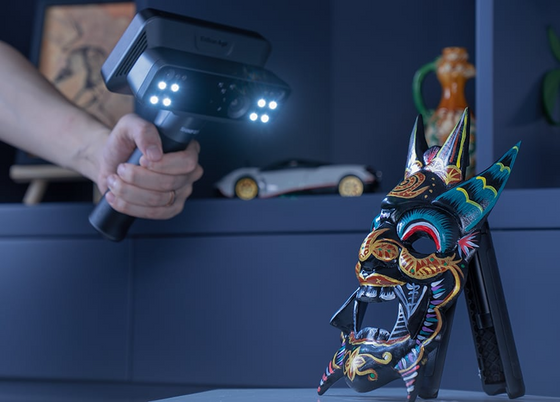
Shop3D.ca Open House: EinScan Rigil 3D Scanner - Technical Training & Demo
August 19, 2025
Join the Shop3D.ca technical team for an interactive demo of the new EinScan Rigil 3D scanner. Learn the ins and outs of professional 3D scanning, and bring a medium-sized object to scan. You’ll leave with your very own 3D model file—just make sure your item is light enough to handle and can be rotated during scanning.
![[Exclusive Webinar] Scan, Print, Maintain, Train: End-to-End Solutions with Shop3D](http://shop3d.ca/cdn/shop/articles/webinar_-_services_560x.jpg?v=1751648502)
[Exclusive Webinar] Scan, Print, Maintain, Train: End-to-End Solutions with Shop3D
July 04, 2025
Shop3D goes beyond sales and distribution of cutting-edge 3D printing equipment - we also offer a full range of end-to-end services to help you make the most of your 3D printing investment. Join our webinar on Thursday, July 17, 11am ET, to discover our range of solutions.
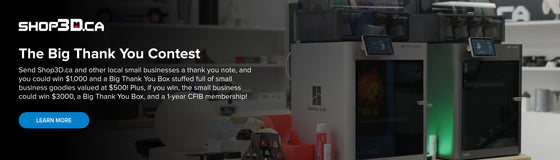
Send us a thank you for a chance to win BIG!
July 02, 2025
Send Shop3D.ca and other local small businesses a thank you note and you could win $1,000 for yourself and $3,000 for the small business you thank. Plus, you both win a Big Thank You Box stuffed full of small business goodies!