Producing customized fashion solutions with Ultimaker 3D printers
November 01, 2018
Florenradica is an Italian design company that fabricates prototypes and end-use parts for fashion houses. Their portfolio of products includes bags, shoes, buttons, jewelry, accessories and more. Florenradica has a background of traditional woodworking but their needs grew, and they ran into the challenge of delivering on high volume orders. How could they reduce physical labor while maintaining high levels of detail and quality? This initiated their transition from traditional to digital manufacturing.
Some of their designs were not able to be replicated with CNC machines and they needed a solution that provided extreme detail with reliable and consistent results. Their first foray into additive manufacturing involved them using budget FFF 3D printers but the printers required a lot of maintenance and experimentation to get reliable results. With 6-60 hour prints, they couldn't spend that time tinkering!
Then they tried Ultimaker. Starting with the Ultimaker 2, results were significantly more accurate and reliable meaning they could depend on the machines. Now they run a printing farm of 27 Ultimaker 2+, 13 Ultimaker 3s and two Ultimaker S5 Studio large format printers. The process starts with modeling in CAD and slicing in Cura, then printing the files in-house. The dual extrusion capabilities of the Ultimaker 3 and S5 printers allow for the use of dissolvable PVA support for easy post-processing which involves collecting the parts, dissolving the supports, sanding, priming, gloss painting and varnishing.
While 3D printed parts have become a significant part of their business (40% of all sales are Ultimaker printed parts) they have not abandoned traditional woodworking entirely. Having printers running means they can do simultaneous production of hundreds of items per day, with predictable lead times.
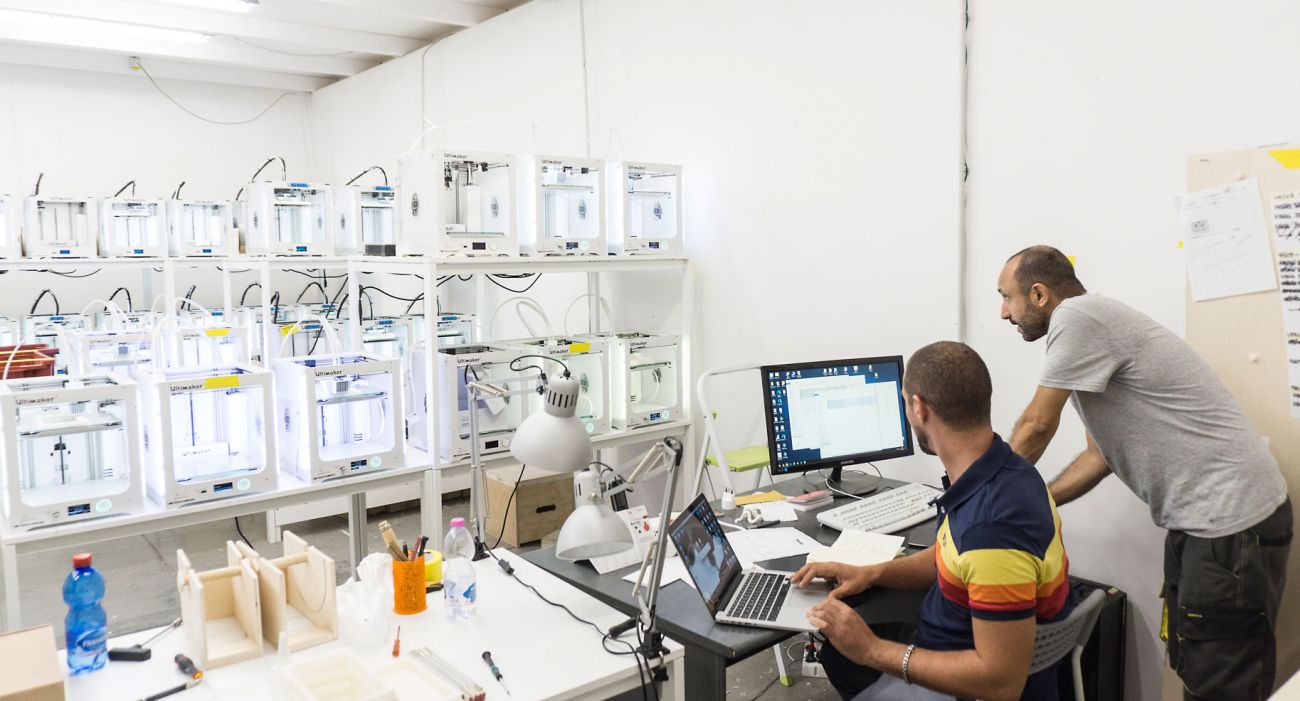
Also in News
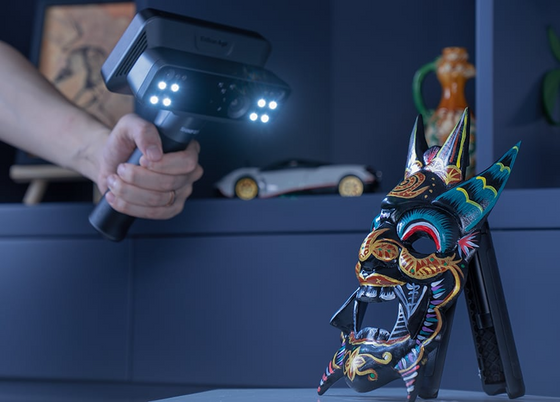
Shop3D.ca Open House: EinScan Rigil 3D Scanner - Technical Training & Demo
August 19, 2025
Join the Shop3D.ca technical team for an interactive demo of the new EinScan Rigil 3D scanner. Learn the ins and outs of professional 3D scanning, and bring a medium-sized object to scan. You’ll leave with your very own 3D model file—just make sure your item is light enough to handle and can be rotated during scanning.
![[Exclusive Webinar] Scan, Print, Maintain, Train: End-to-End Solutions with Shop3D](http://shop3d.ca/cdn/shop/articles/webinar_-_services_560x.jpg?v=1751648502)
[Exclusive Webinar] Scan, Print, Maintain, Train: End-to-End Solutions with Shop3D
July 04, 2025
Shop3D goes beyond sales and distribution of cutting-edge 3D printing equipment - we also offer a full range of end-to-end services to help you make the most of your 3D printing investment. Join our webinar on Thursday, July 17, 11am ET, to discover our range of solutions.
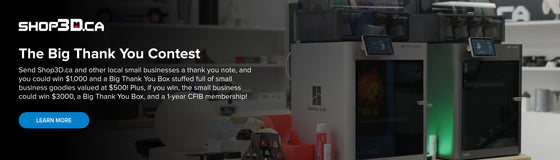
Send us a thank you for a chance to win BIG!
July 02, 2025
Send Shop3D.ca and other local small businesses a thank you note and you could win $1,000 for yourself and $3,000 for the small business you thank. Plus, you both win a Big Thank You Box stuffed full of small business goodies!